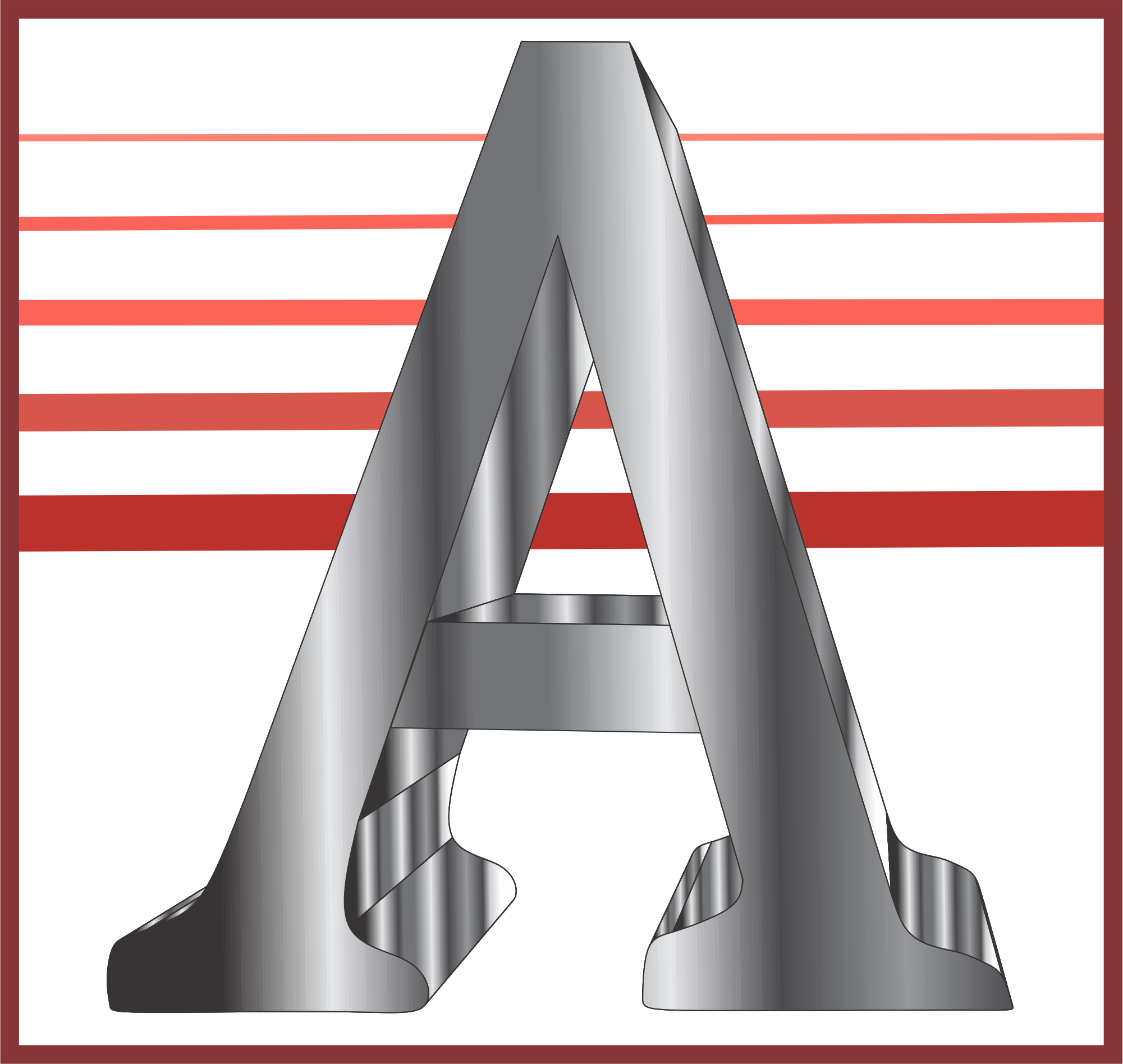
Distinct from investment casting, initial costs of forging dies for developing a metal components in closed die forging is quite high, but by comparison, if the parts are in high volume, it is the most cost-effective metal forming methods for the low cost of each part. During closed die forging process, the pressing of workpiece between forging dies will refine the inner grain, and the mechanical properties of closed die forged parts, especially the strength, will be improved. So, when safety factor and strength is considered, like lifting & rigging hardware, closed die forging will be the unique choice. As products are deformed in high precision forging dies, so the toleraces of closed die forging parts are always tight. And surface finish is always good. Normally, we can control closed die forging parts within tolerance +/- 0.5mm. In this way,this forging technic is a net or near net shape process that requires less or no machining.
So for same parts made in forging and casting, there will be aobvious advantages of closed die forging for its less machining cost. Material is saved. If you learn about closed die forging, then you will know the only waste of material during forging process is the flash. Such flash will be moved by trimming die, and you will be a finished forging blank after that. Thus we can see the flash is the only redundant material, but it can be recycled.
The traditionally designed 4-column hydraulic presses with reinforced steel structure are made for cold forging precision auto/Industrial components in mass production with minimum rejection & maximum tool life through minimum deection, optimum hydraulic circuit design and integrated control of manufacturing processes.
MODEL | ABXC-400 | ABXC-500 | ABXC-600 | ABXC-800 | ABXC-1000 | ABXC-1200 | ABXC-1500 | ABXC-2000 | |
---|---|---|---|---|---|---|---|---|---|
Pressing capacity | TON | 400 | 500 | 600 | 800 | 1000 | 1200 | 1500 | 2000 |
Pull-out capacity | TON | 30 | 40 | 50 | 60 | 80 | 80 | 100 | 120 |
Working Table area LR x FB | mm | 600X800 | 650X800 | 750X900 | 900X1050 | 950X1100 | 1000X1200 | 1100X1350 | 1200X1500 |
Stroke | mm | 400 | 450 | 500 | 600 | 600 | 700 | 800 | 1000 |
Daylight opening | mm | 1150 | 1200 | 1250 | 1300 | 1300 | 1400 | 1400 | 1800 |
Decending speed | mm/sec | 200 | 200 | 200 | 175 | 175 | 175 | 150 | 150 |
Pressing speed | mm/sec | 10 to 15 | 10 to 15 | 10 to 15 | 10 to 15 | 10 to 15 | 10 to 15 | 10 to 15 | 10 to 15 |
Ascending speed | mm/sec | 200 | 200 | 200 | 180 | 180 | 180 | 160 | 160 |
Top & Bottom Die Cushion Capacity | TON | 100 | 100 | 150 | 150 | 200 | 200 | 250 | 300 |
Cushion stroke | mm | 40 | 50 | 60 | 75 | 75 | 90 | 100 | 125 |
Motor | HP | 50 | 60 | 60 | 75 | 100 | 125 | 150 | 200 |
Design & Specification shown here are indicative & are subject to change without prior notice